本文探讨了与原始20×50材料相比,从新的标准20×50产品中去除65目以下颗粒对性能的影响。
Stephen Ashlock
研究和技术部门总监兼陶瓷工程师
美国蓝晶石矿业有限公司
Austin Scheer
Ceramic Engineer , Kyanite Mining Corporation
美国蓝晶石矿业有限公司陶瓷工程师
摘要
最近一项使用弗吉尼亚莫来石的试验显示,20×50材料粗砂中的滋扰性粉尘量高于预期。为此,美国蓝晶石矿业有限公司对现有的筛分生产过程进行了调整,以去除65目以下的莫来石和更小的颗粒。本文探讨了与原始20×50材料材料相比,从新的标准20×50材料产品中去除65目以下颗粒对性能的影响。在旋转滚筒砂光机和流化床中,对比了两种粗砂的测试数据和可比数据。
引言
几十年来,弗吉尼亚莫来石™一直作为熔模铸造行业的细粉和粗砂使用。最近对20×50材料粗砂产品的一次试验引发了客户对雨水塔中产生的粉尘量的评论。据报告,这些粉尘给操作员带来了不便。美国蓝晶石矿业有限公司(KMC)被要求调查这一问题,并研究是否可以对材料进行改进,以减少员工对这些细粉的接触。历史数据显示,KMC的20×50材料莫来石粗砂通常含有20%-30%的筛下物(-50目),且处于粒度规格的下限。因此决定,由于该产品中的细粉过多,需要采用更严格的规格要求。
减少细粉的任务交给了工厂。工厂首先尝试改变筛网大小以调整细粉的数量(定义为能通过50目筛网的颗粒)。他们确实能够生产出含有较少细粉的材料,但为了达到理想的筛分效果,不得不大幅降低进料速度。多次尝试改变筛网大小和进料速度后,效果仍然有限。弗吉尼亚莫来石TM是通过煅烧弗吉尼亚蓝晶石TM制成的,弗吉尼亚蓝晶石TM是一种刀片形状的矿物。经过转化过程后形成的莫来石保持了这种刀片形状,形成了具有高长宽比的单个晶体。这给筛分过程带来了挑战,因为刀片形状的颗粒可能在翻转时通过筛网,但在其他方向上则可能太大而无法通过。降低进料速度会导致筛网上产生更高的振动,从而增加了颗粒以端面方式通过筛网的数量。
经过一些内部研究后,KMC向两家筛网供应商寻求建议。在两家供应商的设施中进行了试验,以找到正确的解决方案。最终,对以下三个方面进行了改进:
将底部筛网的大小改小,以使细粉更容易通过
在筛网堆的中间增加了一个额外的筛网。这有助于减轻最终筛网的负荷并提高筛分效率
调整了配重的位置,以控制产品弹跳和筛网上方的停留时间
通过这些改变,工厂能够生产出筛下物中细粉含量低于6%的产品,同时筛上物(20目)中细粉含量也低于1%。新的设置还允许工厂以仅略低于旧款“粉尘较多”产品的生产速度生产这种材料。在成功证明可重复之后,提出了对20×50规格的更改,具体如表1所示。

KMC希望确保去除这些细粉不会对产品的性能产生负面影响。文献综述显示,有许多研究探讨了细粉粒度分布变化对浆料流变性的影响,1,2,3但关于粒度对粗砂影响的研究较少。研究表明,增加粒度往往会导致壳型更厚、煅烧后抗折模量(MOR)更弱以及渗透性增加。4,5这些工作大多是在熔融硅质粗砂上进行的,关于改变铝硅酸盐粗砂粒度分布的影响的数据很少。因此,决定在KMC的研发实验室中对旧材料和除尘材料进行测试,以在另一次试验之前进行评估。
测试设置
本研究的主要目的是确定细颗粒对20×50粗砂的影响。KMC希望验证去除-50目颗粒不会对粗砂的性能产生严重影响。为此,使用了两种粗砂。第一种粗砂是KMC多年来一直使用的标准产品。第二种是除尘后的新标准产品。为了清晰起见,在图表和表格中,旧材料标记为“Old”(旧),新材料标记为“DD”。粗砂是通过旋转滚筒砂光机(RD)或流化床(FB)涂覆的,因为这两种方法在行业中都很常见。这创造了四种独特的情况:使用旋转滚筒涂覆的旧材料、使用流化床涂覆的旧材料、使用旋转滚筒涂覆的除尘材料,以及最后,使用流化床涂覆的除尘材料。在所有层中都使用了20×50粗砂。两种涂覆方法都启用了集尘系统。
在涂覆开始之前以及每层之间,每种粗砂都经过了Ro-Tap筛分机的筛分。在每层涂覆后进行筛分是为了检查是否有细粉流失到周围环境中(成为滋扰性粉尘)。
由于这是一次粗砂测试,每层所使用的浆料都保持一致。这种浆料是基于200目弗吉尼亚莫来石TM的浆料,其中使用了大颗粒胶体二氧化硅和乳胶聚合物。添加了表面活性剂以帮助润湿蜡质,并使用了消泡剂来消除气泡。在整个壳型构建过程中,所有涂层都使用了这种浆料。使用Zahn EZ #5杯测量的粘度保持在20秒。这些铸条由8层浆料和粗砂制成,之后涂上一层封闭层。
大约12×1×0.125英寸的金属条被浸入未填充的蜡中以创建MOR样品的基材。对于渗透性样品,也在较大的12×2×0.125英寸的铸条上进行了相同的操作。在浸涂开始之前和每次浸涂之后,铸条都被放置在温度和湿度控制柜中。铸条在柜中保持干燥至少4小时。在每次浸涂之前,用油漆刷刷掉松散的粗砂。
MOR测试根据ASTM C133-97(2015)标准进行,对未烧制和烧制后的铸条都进行了三点弯曲测试。烧制后的铸条在箱式炉中以2400°F(1315℃)的温度烧制,并保持两小时。测试时,铸条的平蜡面朝下并处于拉伸状态。每种情况(未烧制和烧制)都测试了10根铸条。
渗透性测试在Buntrock Industries Inc.技术实验室进行,使用了在第52届ICI技术会议和展览会上介绍的渗透性测试方法。6选择这种测试方法是为了避免乒乓球(测试中的小球)燃烧不充分的问题。
结果与讨论
筛分
在每次涂抹浆料之前都进行了筛分取样。表2显示了所使用的旧材料和除尘材料的比较。除尘的粗砂材料比旧粗砂更粗。两个旧20×50样品显示,-50目颗粒的含量要高得多,与预期一致。除尘材料还含有大量+30目的材料,这在旧材料中是不存在的。这种较粗的粗砂应该有助于改善壳型构建。这一点在MOR铸条的厚度上得到了体现,下面将进一步讨论。

在浸涂开始时,我们采集了筛分样品以观察粒度分布的变化。图1显示了四种条件下粗砂的变化情况。总体来说,流化床粗砂中的细粉(定义为-50m)数量并没有发生显著变化。中间层的数据存在一些不一致性,但在两种情况下,从第一层到最后一层,材料的变化都小于1%。
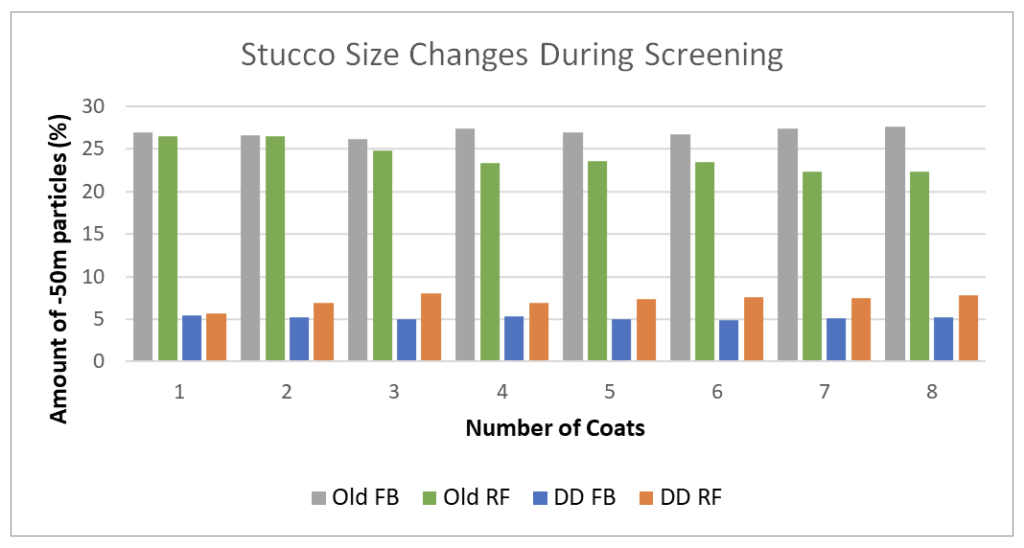
旋转滚筒砂光机中的材料随时间发生了变化。从首次涂覆到最后一次涂覆,旧材料损失了一些细粉(4.16%),这些细粉流失到环境中。这种细粉的损失是线性的,很可能是由于环境中的滋扰性粉尘损失或被除尘系统吸走所致。相比之下,在除尘材料中,随着测试的进行,细粉的数量略有增加。与首次涂覆相比,最后一次涂覆时细粉数量增加了2%。细粉的数量在第三层涂覆时达到最高水平,并在测试剩余部分保持稳定。这可以用莫来石的易碎性质和形状来解释。当蓝晶石转化为莫来石时,晶体发生膨胀,使其成为一种更易碎的材料。当粗砂落在旋转滚筒砂光机内部的筛网上时,尖角脱模,较弱的颗粒就会破碎。到第三次粗砂涂覆时,这些较弱的颗粒似乎已经破裂,导致数据出现平台期。同样的现象可能也发生在旧的、更容易产生粉尘的粗砂中,但由于滋扰性粉尘损失,这一现象并未引起注意。
在每个涂覆过程中,我们对四种条件都进行了录像,以观察空气中飘浮的滋扰性粉尘量。不出所料,视频显示,在使用旧粗砂时,两种涂覆方法都会释放出更多的粉尘。在滚筒砂光机的边缘上,可以明显看到一层细目物料覆盖,而使用除尘后的材料时则没有观察到这种情况。
筛分测试的结果表明,除尘后的材料不会给操作人员带来很多滋扰性粉尘问题。另一个好处是,进入除尘系统的粉尘减少,而袋装产品中有更多的部分将直接用于铸件,不会流失到除尘器中。这也意味着减少了清理袋式除尘器的工作量,从而节省了时间和成本。
旧粗砂的粉尘损失数据表明,在将新材料引入旋转滚筒砂光机后,操作人员需要长时间在该区域工作之前,应先将粉尘较多的粗砂在研磨机中运行一段时间。这样做可以让除尘系统从粗砂中抽离出部分细粉,从而减少操作人员接触粉尘的风险。执行这一步骤所需的额外时间需根据具体情况进行评估。
MOR
为探究粉尘对壳型强度的影响,进行了抗折模量(MOR)测试。测试数据如图2所示。除使用流化床工艺的除尘粗砂外,其余四种绿色条件下的MOR值均相近。然而,使用流化床工艺的去尘灰泥的MOR值比采用相同方式涂覆的旧粗砂低16%。这一显著差异并不在预期范围内,因为旋转滚筒砂光机使用这两种粗砂生产出的铸条在生坯强度上相似。为确认或更新这一结果,需进行进一步测试。
图2:使用抗折模量来检查除尘对绿色和烧制后状态下壳型强度的影响。
在烧制状态下,无论采用哪种涂覆方法,旧粗砂的MOR都高于除尘材料。使用旋转滚筒砂光机时,旧粗砂的强度比除尘粗砂高10.3%,使用流化床时则高8.3%。据了解,更宽的粒度分布能制造出颗粒堆积更好的陶瓷体。7由于颗粒大小的更大变化,小颗粒可以填充大颗粒之间的间隙,减少陶瓷颗粒之间的孔隙大小。更多的细粉存在也增加了莫来石粗砂的总体表面积。孔隙空间减小与表面积变大相结合,会导致烧制过程中的烧结程度高于粒度分布较窄的较粗粗砂。这将形成更坚固的结构并产生更高的MOR值。由于烧制后的MOR较低,除尘粗砂制成的壳型比旧材料更容易脱模。
最后,使用流化床制作的铸条的MOR值低于使用旋转滚筒砂光机制作的铸条,无论使用哪种粗砂。这可以归因于粗砂渗透到浆料层的深度。旋转鼓式涂覆方法允许粗砂在接触湿浆料之前落下并获得动能。这使得粗砂颗粒能够更深入地渗透到浆料层中,更多的颗粒被浆料覆盖,形成更强的结合力。8这一结果与其他研究者的研究结果相一致,他们比较了使用流化床与雨淋砂光机创建的壳型的MOR差异。8,9,10
壳型厚度
从MOR铸条的厚度测量来看,使用除尘粗砂在相同涂层数量下形成了更厚的壳型。平均而言,较粗的除尘粗砂壳型比使用旧粗砂的壳型大约厚6%。这一结果符合预期,因为文献中已经报告了类似的结果。5除尘粗砂中+30目材料的含量较高,本身会倾向于形成更大的涂层,但除尘也有助于壳型的构建。在使用旧粗砂时,无论采用哪种涂覆方法,都明显有较多的空气粉尘。这些粉尘一旦引入砂光机就会开始覆盖湿铸条,降低较大颗粒正确粘附的能力,导致形成较薄的壳型。
正如预期的那样,使用流化床涂覆的除尘粗砂铸条厚度最高。研究表明,流化床产生的壳型比雨淋式砂光方法产生的厚度更高。9如前所述,在雨淋情况下,粗砂下落时获得的动能增加,使其能够更深入地嵌入浆料层中。这减少了粗砂突出的高度,从而形成了较薄的壳型。
渗透率
遗憾的是,由于KMC实验室的问题,在发布时并未提供渗透率数据。这些数据将在技术会议上进行展示。
然而,文献中已经表明,增加粒度会增加壳型的渗透率。Whitehouse/Snyder的研究还显示,添加50×100的粗砂对壳型的渗透率有负面影响。5因此,假设较粗粒度的除尘粗砂创建的壳层比使用旧粗砂制成的壳型具有更高的渗透率。
对文献综述还表明,使用雨淋砂光机涂覆粗砂创建的壳型比使用流化床创建的壳型具有更低的渗透率。8这是因为从较高高度落下的冲击能够增加动能。厚度测试数据已经显示了接触时增加动能的效果。因此,假设由于同样的原因,在旋转滚筒中制作的样品将比流化床中制作的样品具有更低的渗透率。
结论
通过提高对-50目颗粒的规格要求,达到了减少滋扰性粉尘的主要目标。在使用旧粗砂时,粉尘会流失到环境中,但在旋转滚筒或流化床中进行浸涂序列时,除尘材料中的细粉数量几乎没有变化。在旋转滚筒中使用除尘材料时,小颗粒的数量略有增加,并在第三次涂覆时达到稳定水平。这可以归因于莫来石的易碎性。如果不是因为细粉流失到环境中而抹掉了证据,这种现象也会在旧粗砂中出现。
MOR测试表明,从粗砂中去除细颗粒对铸条的烧制强度有负面影响。这可能是一个好结果,因为这样会更容易脱模。除了使用流化床的除尘粗砂外,生坯强度基本保持不变。为确认或更新这一结果,将需进行进一步测试。测试还观察到MOR样品中的壳型厚度存在差异。使用除尘粗砂制成的铸条更厚,表明这种新材料具有更快的壳型构建速度。
总之,除尘粗砂很可能达到了减少滋扰性粉尘的目标,且对最终产品没有产生严重的负面影响。通过减少粉尘流失量,操作人员可以在更清洁的环境中工作,并且除尘系统需要的清洁次数更少,从而节省时间和成本。将进行进一步调查,以确保渗透性没有受到负面影响。
REFERENCES
- Dinger, D. R., Rheology for Ceramists. Dinger. (2010).
- Feagin, R. C., “The Influence of Refractory Particle Size on Slurries and Shells”. Investment Casting Institute, 25th Technical Conference and Expo. 1977.
- Oles, M., “Targeting and Controlling Mold Properties Through Refractory Particle Size Blending”, Investment Casting Institute, 53rd Technical Conference and Expo. 2005.
- Nanda, I. P., “The Effect of Stucco Sand Size on the Shell Mould Permeability and Modulus of Rupture (MOR)”, Journal of Aeronautical Science and Engineering. 13. 2018.
- Whitehouse, C., and B. Snyder, “Healthy Shell: Wide Distribution Stucco Blends & Their Effects upon Shell Performance, Part II”. Investment Casting Institute, 59th Technical Conference and Expo. 2012.
- Branscomb, T. “A New Method of Measuring Green and Fired Permeability of Investment Casting Shells”. Investment Casting Institute, 52nd Technical Conference and Expo. 2004.
- Dinger, D.R., “Chapter 8 – Influences of Particle Size Distributions on Whitewares Properties and Processing,” Science of Whitewares, edited by V.E. Henkes, G.Y. Onoda, and W.M. Carty, The American Ceramic Society, Westerville, OH, pp 105-115 (1996).
- Dooley, G. et al. “Effect of Stucco Application Method on the Mechanical Performance and Microstructure of Investment Casting Shells”. Investment Casting Institute, 60th Technical Conference and Expo. 2013.
- Jones, S., C. Yuan, and M. R. Jolly, “Fluid Bed and Rain Fall Sanded Shells – An Investigation into Fundamental Structural and Mechanical Property Differences”, Investment Casting Institute, 51st Technical Conference & Expo. 2003.
- Jones, S., C. Yuan, and S. Blackburn, “Fundamental Study of the Microstructure and Physical Properties of Fluidised Bed and Rainfall Sanding Ceramic Shells”, Journal of Materials Science and Technology, 2007. 23(6): p. 706-714.
发表回复